加工灰铸铁深孔件刀具的改进
2013-5-5 来源:齐齐哈尔二机床 作者:李新 王晓东
我公司是生产金切机床的传统企业,在以往加工立式车床的灰铸铁升降箱体传动孔系时,所消耗的机加工工时约为16h,同时加工质量很难保证,已成为制约生产的瓶颈。
加工同样切削量的其他工件所需要的机加工工时为3~4h,如果找到合理的方法,工件加工时间可以大幅减少。加工灰铸铁一般采用YG8硬质合金刀具,但因为本工件孔系尺寸较深,并且φ 95js7孔、φ 102j s7孔都是要求清根的台阶孔,传统的加工方式只能采用斜方刀杆(见图1)。而硬质合金刀具硬而脆,加工时容易产生崩刃现象,所以传统的斜方刀具只能采用高速钢类刀具。高速钢类刀具的缺点主要表现在易磨损,特别是加工灰铸铁类深孔零件时,因产生高热量不能及时排出去,加速了高速钢刀具的刃部磨损。因此机床在加工零件时主轴转速只能在80r/min以下,刀具进给量约为0.10mm/r,也就是工件切削量仅为8mm/min,加工效率非常低。
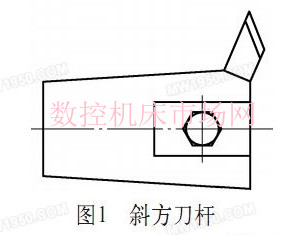
采用硬质合金类刀具受限的根本原因是,斜方刀杆截面积较小,刚性不足易产生刀体颤动,刀具刃部受力不稳导致崩刃。通过对刀块的受力分析(见图2),发现斜方刀杆上刀块主要受与刀具进给方向相反的力,这个方向上的力我们可以分解为两个力。一个是垂直于刀块的力,一个是平行于刀块的力。垂直于刀块的力对刀具的定位没有影响,而平行于刀块的力是使刀块颤动的主要原因。通过以上分析,决定将主要解决两个问题:①解决刀具进给时颤动的问题。②进而将高速钢刀具改为硬质合金刀具。
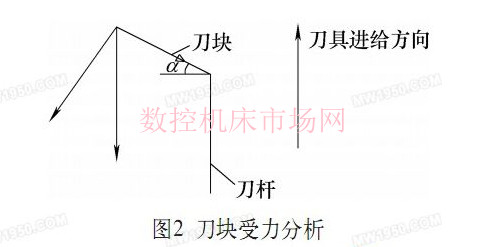
通过实践经验得出刀具与垂直于刀杆方向上的夹角α越小,刀具所受的平行于刀块的力越小(见图2),所以减小刀具与垂直于刀杆方向上的夹角。
第一次改进,使刀块与刀杆的固定槽改为与前端面平行,也就是使刀块与刀杆垂直方向的夹角变为0°,刀块加工成L形, 插入刀杆孔之中并增加了两个固定螺钉,保持刀具进给量0.10mm/r不变,加工零件时主轴转速提高到180r/min,也就是工件切削量为18mm/min。加工效率有所提高但是由于刀具的受力作用产生刀块的颤动,刀具稳定性还是不好。主要问题是主轴转速超过180r/min后打刀的现象很显着,造成平均生产时间远远没有达到理想要求。
针对第一次刀具改进后效果不理想的情况,我们做了第二次改进方案。在第一次方案的基础上在前端开口处保留了5mm的刀杆体不加工掉,其作用是限制刀具在加工零件过程中受切削力而造成左右颤动,进而增加刀具的稳定性(见图3)。同时镗刀块加工成L形(见图4), 插入改进后刀杆孔之中。
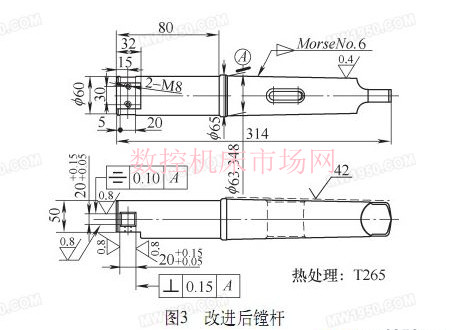
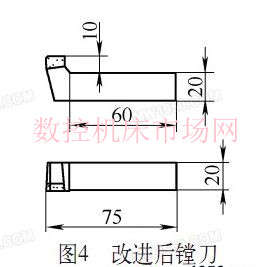
经过改进的刀具在稳定性方面有了显着提高。
这样就使机床在加工过程中主轴转速有了提高的保证,经过试验得到:主轴转速最大提高到200r/min,同时刀具进给量最大提高到0.26mm/r,即切削量为52mm/min,几乎没有打刀的现象出现,就是达到了稳定切削的极限值。此时切削量比改进前的8mm/min,提高了5.5倍。
对2010年9月以后加工升降箱体所用时间进行抽样调查,平均加工时间为3.78h。与开始15.7h降低了75.92%的加工时间,改进取得显着成功。
以上改进主要是改善刀具的安装位置和形态,增加刀具的稳定性,减少切削时引起的颤动;从而达到了高速和大进给量地切削铸铁工件,同时刀具的崩刃现象基本消失,生产效率得到显着提高。需要注意的是:主轴转速200r/min,进给量0.26mm/r,即切削量为52mm/min时,是加工该零件的切削量极限;超过极限值刀具仍会出现崩刃的情况。
投稿箱:
如果您有机床行业、企业相关新闻稿件发表,或进行资讯合作,欢迎联系本网编辑部, 邮箱:skjcsc@vip.sina.com
如果您有机床行业、企业相关新闻稿件发表,或进行资讯合作,欢迎联系本网编辑部, 邮箱:skjcsc@vip.sina.com